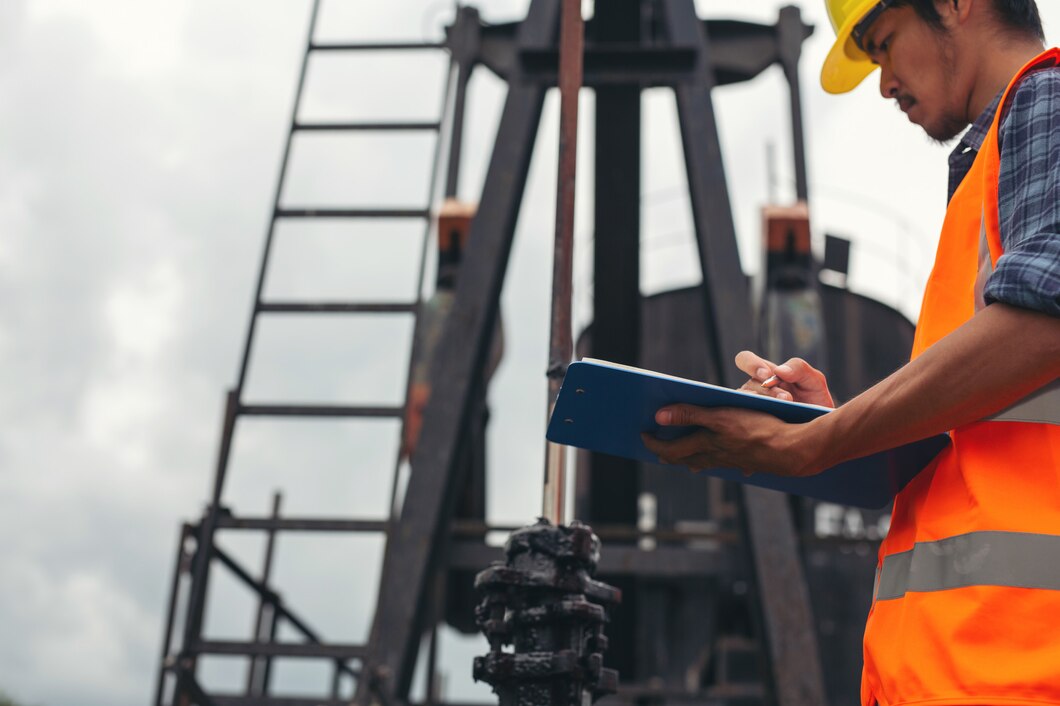
Plant & Machinery Valuation Services: Methods, Importance, and Key Considerations
1. Introduction
Plant & machinery are critical assets for businesses across industries. Whether it’s manufacturing equipment, construction machinery, or specialized tools, these assets require proper valuation for financial reporting, insurance, taxation, and business transactions. Without accurate valuation, businesses may face financial discrepancies, tax issues, or insurance coverage gaps.
The demand for plant & machinery valuation services is growing, as industries increasingly rely on these assets to generate revenue. Whether businesses are buying, selling, insuring, or assessing asset depreciation, professional valuation services help in making informed decisions. However, valuation is complex due to factors like depreciation, technological changes, and market fluctuations.
2. What is Plant & Machinery Valuation?
Definition and Scope
Plant & machinery valuation refers to the process of determining the fair market value of machinery, equipment, and industrial assets. This valuation is essential for businesses that rely on heavy equipment for production and operations.
Industries That Require Valuation
Several industries depend on machinery valuation, including:
- Manufacturing
- Construction
- Mining
- Agriculture
- Oil & Gas
- Transportation
Common Use Cases
- Selling or buying equipment
- Lease agreements
- Financial reporting and audits
- Asset-based lending
3. Importance of Plant & Machinery Valuation Services
Accurate valuation ensures businesses understand their asset worth, helping in:
Financial Reporting and Compliance
Businesses must comply with accounting standards that require periodic asset valuation.
Insurance Purposes
Proper valuation ensures machinery is adequately insured against damage, loss, or theft.
Buying, Selling, and Leasing Decisions
Machinery valuation helps in setting fair prices for sales, purchases, or lease agreements.
Taxation and Depreciation Calculations
Correct valuation helps in tax filings and depreciation schedules to optimize financial planning.
4. Methods of Plant & Machinery Valuation
Three primary methods are used for plant and machinery valuation:
- Cost Approach – Determines value based on the cost to replace or reproduce the asset.
- Market Approach – Compares the asset’s value to similar equipment in the market.
- Income Approach – Evaluates the machinery’s potential to generate income.
Each method is used depending on the purpose of valuation and availability of data.
5. Cost Approach to Valuation
The cost approach is based on the principle of substitution, meaning the value is determined by how much it would cost to replace the asset with a new one of similar functionality.
Key Methods:
- Replacement Cost Method – Estimates the cost of replacing the asset with a new equivalent.
- Reproduction Cost Method – Estimates the cost to recreate the exact same asset.
Depreciation Factors Impacting Value
- Physical wear and tear
- Functional obsolescence
- Economic obsolescence
6. Market Approach to Valuation
The market approach determines the value of machinery by comparing it to recent sales of similar equipment.
Steps in Market Approach:
- Identify comparable machinery in the market.
- Adjust for differences in condition, age, and location.
- Estimate fair market value based on comparable sales.
Challenges:
- Limited market data for specialized equipment.
- Variability in machinery conditions affecting pricing.
7. Income Approach to Valuation
The income approach values machinery based on its ability to generate income. This is often used when equipment is leased or generates revenue.
Methods:
- Capitalized Expected Income – Estimates future earnings and applies a capitalization rate.
- Discounted Cash Flow (DCF) Method – Forecasts future cash flows and discounts them to present value.
This approach is useful for assets with a clear revenue stream but is less effective for general-purpose machinery.
8. Key Factors Affecting Machinery Valuation
Several factors influence valuation, including:
- Age and Condition – Older machines lose value due to wear and tear.
- Technological Advancements – Newer models can make older equipment obsolete.
- Market Demand and Supply – High demand can increase resale value.
- Economic and Industry Trends – Economic downturns can reduce machinery value.
All Categories
Recent Posts
5 Common Mistakes to Avoid When Using Business Valuation Services
Top 10 Benefits of Professional Business Valuation Services
Trusted Valuation Experts in India Delivering Powerful Business Insights
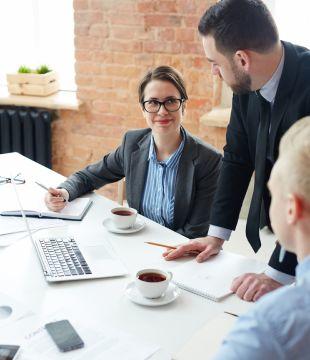